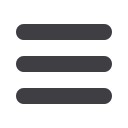
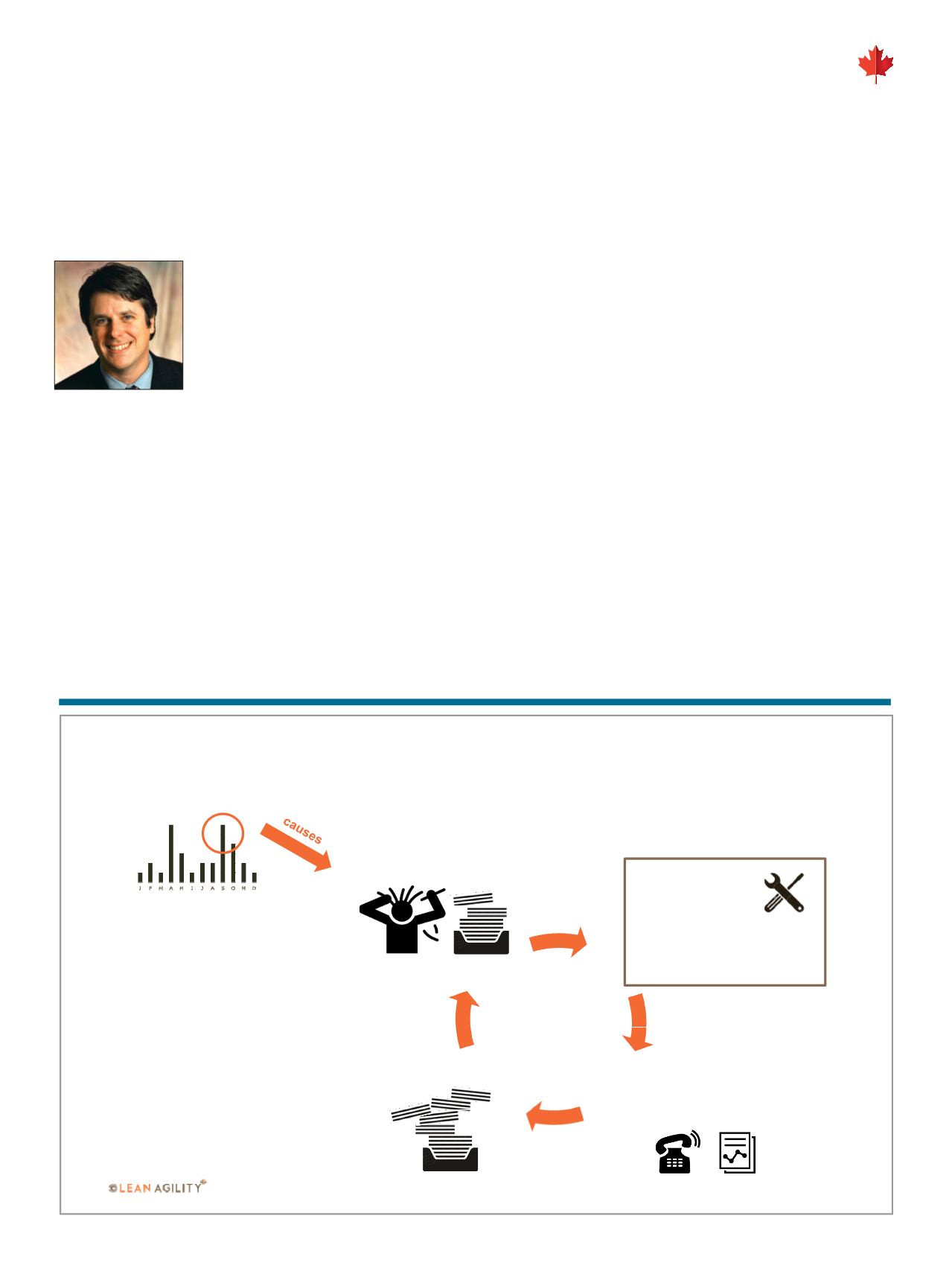
How backlogs occur:
E
ver feel like that ever-growing
backlog of un-started or un-fin-
ished files has a life of its own?
It can be hard to make progress
on it, especially while clients keep call-
ing, new requests come in and staff are
busy creating backlog reports. You bring
in temporary help to fix the problem but it
doesn’t help and you’re left with low staff
morale and an even larger backlog. If only
you could blow up that backlog.
Others have and you can too – here’s how.
January 2016 //
Canadian Government Executive /
9
Management
Craig
Szelestowski
Lean Dynamite for Backlogs
1. Increase in
volume of work
3. Team spends its reduced
capacity on non-value
added, preventable, work
made
worse by
4. Team spends capacity on:
•
Client progress-chasing
calls
•
backlog reporting
• Fixing errors
• Clarifications
• Re-drafting
• False starts
• Looking for information
• Unnecessary approvals
• Excessive processing
2. Overwhelmed team,
thus reduced
productivity
made
worse by
allowing
5. Fewer files finished,
a growing backlog
repeat
Steps 2-5,
fall further
behind
Lean thinking provides dynamite to
clear away the spiral of steps leading to
backlogs and prevent them from coming
back once and for all.
Step 1.
Increase in Incoming
Demand
In Lean, variation in demand is one of the
key “wastes”. I coached a public servant
from a provincial Ministry of Transpor-
tation who had taken a Lean Facilitation
course that I co-instruct. He was working
with a program area process that grant-
ed renewals of permits for businesses to
operate commercial vehicles. They had
a backlog of over 4,000 files and a 90+
day waiting period to process renewals.
Staff were stressed and clients, anxious
to keep their businesses running, were
unhappy with long delays. One of the
causes of the backlog was a variation in
demand for permits during high seasons:
April, when landscaping companies pre-
pare their trucks for the new season and
September, when snow-clearing compa-
nies do the same. Try as they might, staff
in the Renewals process could not deal
with this sudden increase in demand,
and built up backlogs that they tried
in vain to reduce before the next peak
month hit.
Note that the seeds of backlogs are not
only planted by unaddressed “high sea-
sons”. An unanticipated reduction (or
variation) in the number of staff avail-
able to perform even a steady amount of
work can also lead to a backlog. Either
way, the unaddressed variation in incom-
ing client demand, or supply of staff to do
the work, is where the spiral begins.